Four Common Features of Industry 4.0
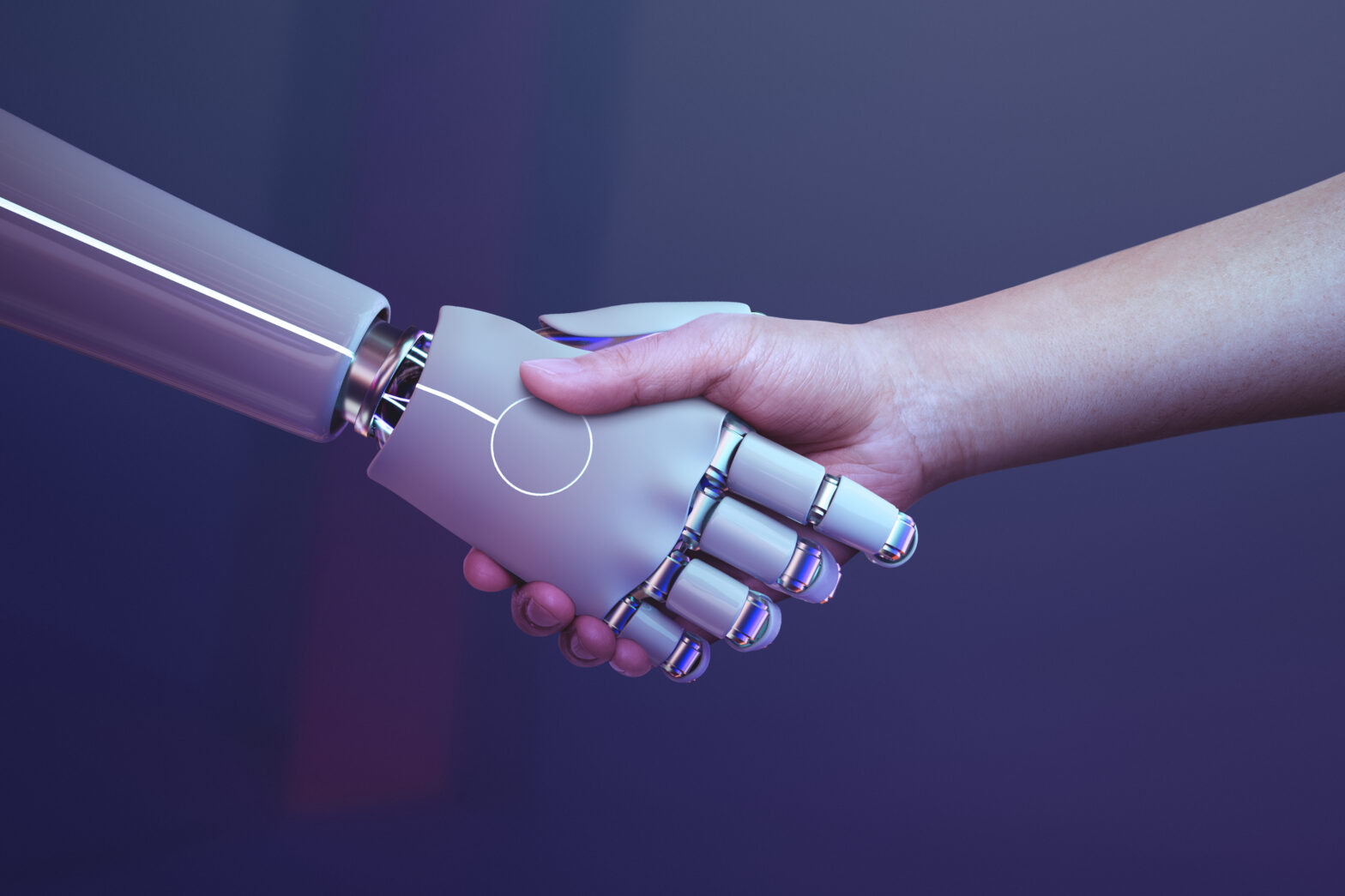
Industry 4.0 brings the next gear change in manufacturing through the digital transformation of value chains interconnecting the physical, digital, and virtual worlds.’’
Marcos Kauffman: Director of the Institute for Advanced Manufacturing and Engineering (AME) at EUIBIC Coventry University
Despite the lack of a clear definition, the proponents of Industry 4.0 have been consistent since its conception to identify four main and distinct characteristics at its core:
Vertical integration
To create smart factories, which are at the centre of Industry 4.0, smart technologies have to be deployed in a coordinated and purposeful manner. The smart factories must be connected in a coherent way to create a link between the products, the processes, the machines, the production lines, the factory and the business. At the core, vertical integration in this context is used to refer to cyber-physical systems (CPSs), which connect an entire factory and enable maximum efficiency and flexibility to react quickly to customer requirements and unexpected disruption.
Horizontal integration
The next level of integration is aimed at creating a network of vertically integrated and optimized businesses that enables efficient value creation across the value chain. An example of a horizontally integrated value chain that springs to mind is one where a car factory is connected to its customers and suppliers across the value chain. The customer uses an online vehicle configuration tool which allows the selection of customized options for the vehicle. Upon the configuration of the vehicle, the customized options are converted into product and process requirements which are distributed in near real-time across the value chain for the efficient production and assembly of the car. This level of integration also results in several opportunities for the creation of new business models across industries and countries, making for global networks.
End-to-end engineering
The term end-to-end engineering, sometimes referred to in manufacturing as ‘cradle to grave’, is used in this context to describe engineering across the entire product lifecycle: from initial product concept, product development and product development, all the way to manufacturing, customer use, maintenance and end of life activities such as repairing, repurposing or recycling. This requires the whole engineering process to be connected, oftentimes across organizations involved in the process. One example of end-to-end engineering in action is found in how new battery packs for electric
vehicles are designed with the entire lifecycle and, in some cases, even with the second life in mind. This may involve the integration of an engineering house with expertise in battery design, the car manufacturer, the battery manufacturer and the recycling business to work together in designing the life of the product. So batteries are designed to have a second life, i.e., after its useful life in a vehicle, as part of a system for power storage for solar-powered homes.
Rapid growth in manufacturing
The three characteristics mentioned above are associated with the fourth which is the increase in the pace of growth in manufacturing. This growth is realized by the improved speed of development and efficiency across engineering and operations across the value chain.